A day in the life of Shoreline Aviation’s line team
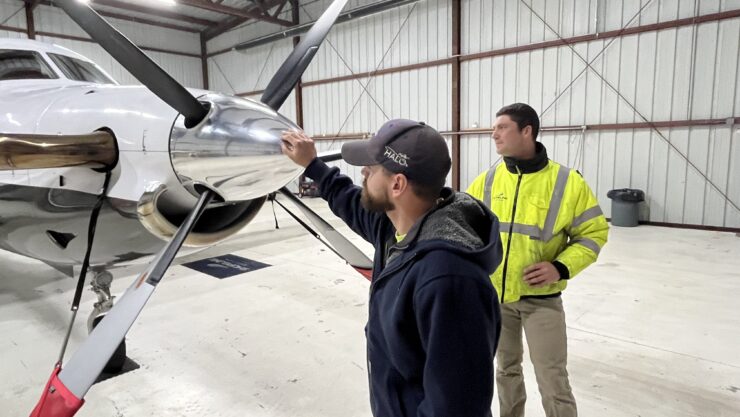
Line Service Manager Steve Dery, left, and Assistant Airport Manager Ben Garman inspect the Shoreline Aviation charter fleet’s Pilatus PC-12NG.
We thought it would be interesting to offer a glimpse into some of the inside moves that take place to prepare aircraft for charter flights.
~~~~~~~
The two friends and work mates step out the back door of the terminal building at KGHG, through the gate of the chain link fence that contains visitors (and airport pups) to the viewing lawn, and onto the ramp that leads to the hangars, where they’ll begin their aircraft prep duties for the day.
KGHG is the ICAO (International Civil Aviation Organization) location indicator for Marshfield Municipal Airport. The FAA location identifier is GHG. The “K” in KGHG is a regional identifier; “K” stands for the contiguous United States. Shoreline Aviation Inc. is the airport’s fixed base operator (FBO) – or in essence the company that manages the airport for the town of Marshfield.
Assistant Airport Manager Ben Garman has worked at one place since he was a student at Bridgewater State University – Shoreline Aviation. The South Shore native, whose dad flew for UPS, majored in Aviation Management, came onboard as a Line Service Specialist, and grew on the job with what he calls a “great team.” Ben spends most of his time seeing that ground operations are carried out, such as managing parking, fueling, towing, and hangaring aircraft, as well as handling fuel sales and manning the operations desk.
Line Service Manager Steve Dery joined Shoreline a couple of years ago. Like Ben and many other Shoreline associates, Steve’s aviation roots grew close to home. His dad was a pilot and used to take him on adventures in a high-wing Cessna 180. He began flight school training at Vermont Technical College, where he studied professional pilot technology, and is continuing his training at Shoreline, where he hopes to become a staff pilot. He previously served as lead supervisor at the former Barnstable Municipal Airport (now Cape Cod Gateway Airport).
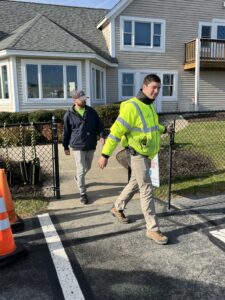
Assistant Airport Manager Ben Garman, front, and Line Service Manager Steve Dery depart the Marshfield Municipal Airport terminal building to begin aircraft preparations for the day’s charter flights.
The process begins
It’s a windy, but warm and sunny fall day at the airport. Ben and Steve are starting their preparation procedures for two fleet aircraft that are scheduled to take off that day.
Shoreline Aviation performs several functions, both in managing the airport and in operating a savvy aviation business. The company provides aircraft sales and acquisition brokerage services, maintenance management, a maintenance service center (including authorized Piper and Diamond service and capabilities for several prop, turbo-prop, and jet aircraft), fuel and tiedown service, and private chartering with its staff of certified pilots and turbo-prop and jet fleet. You can learn much more about Shoreline here: www.shorelineaviation.net.
This day is all about prepping procedures for a Pilatus PC-12 NG turbo-prop, which was going to New York to pick up passengers to bring back to Marshfield, followed by a Citation 560XL jet, which was set to take a group to wonderfully warm Florida.
Ben and Steve stroll across the ramp and past the jet hangar to the Pilatus hangar, directly behind Shoreline’s Maintenance Department. They step through the doorway inside the hangar, where they flip the large hangar door latches and pull the drop pins at the center. Ben sticks his head back through the door and looks up and down the tarmac.
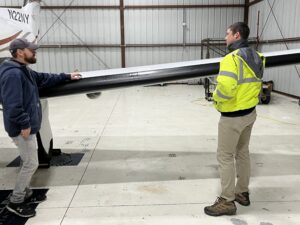
Line Service Manager Steve Dery, left, and Assistant Airport Manager Ben Garman inspect the Shoreline Aviation charter fleet’s Pilatus PC-12NG as part of their preflight preparations.
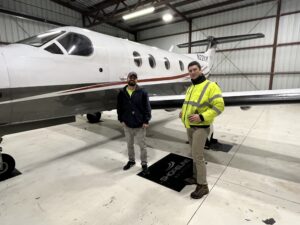
Line Service Manager Steve Dery, left, and Assistant Airport Manager Ben Garman pose with Shoreline Aviation charter fleet’s Pilatus PC-12NG.
“We have to open the regular door and look out to be sure no one or any aircraft are outside, as the hangar door folds in half as it lifts and bends out,” Ben says. “We always monitor the hangar doors going up and down in case it has to be stopped for any reason.”
Bright sunlight fills the hangar, and the sparkling clean plane (another line crew function) stands handsome, rugged and strong as the PC-12’s workhorse reputation would suggest.
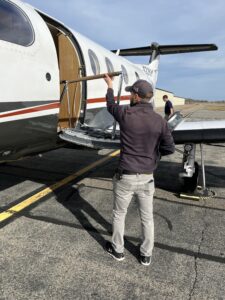
Line Service Manager Steve Dery lowers the stairs of the Pilatus PC-12NG.
“We’ll do a walkaround to make sure the plane is as clean as possible,” Steve says. “I’ll check the body, and the wing’s leading edge to be sure there’s no bumps. And we want to make sure the windshield is clean for the pilots’ sake – we want to make sure they can see outside!” he adds with a laugh.
The Line Service Manager then performs an interior inspection. He pops the door open, careful to catch the dropping steps. Inside he checks each seat and the windows for cleanliness, makes sure all armrests open properly, and checks that the seatbelts are set just so. Likewise in the cockpit – all clean, in order, and set to go.

Assistant Airport Manager Ben Garman powers up Shoreline’s electric tug to prepare it to move the fleet’s Pilatus PC-12NG from its hangar.
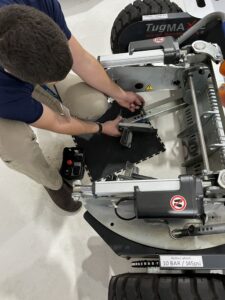
Assistant Airport Manager Ben Garman adjusts the arms of Shoreline’s electric tug to prepare it to move the fleet’s Pilatus PC-12NG from its hangar.
Tug time
So – time to move the turbo-prop aircraft out to the ramp. But unlike a small single prop that can simply be pushed out of a hangar, this five-tonner needs an assist. Enter the tug.
Ben is already across the way to the jet hangar, where a pair of electric tugs park. He turns on the battery powered, remote controlled tug. Its adjustable arms actually pick up the nose of an aircraft at the front wheel. These tugs can maneuver an aircraft just so. In the jet hangar that means they can fit three Citation jets like three siblings all nestled in a double bed.
Ben guides the tug under a jet wing, out the back door and across to the waiting Pilatus. He spins it around and backs it in to the lead wheel. The tug’s arms envelop the wheel in their powerful grip and then lift the wheel off the ground.
The tug is moved at a calm, walking pace.
In fact, all movements are completed as calm, deliberate steps. Ben explains.
“For the departure process, the three principles are, we want to make sure everything is done safely and also efficiently so that we’re not rushing,” Ben says. “We tend to start two hours prior to the departure of the aircraft. That way we can do everything at a nice reasonable pace so no one’s rushing anything, and everything gets done safely.”
The Pilatus PC-12 NG (Next Generation) is the successor to the original PC-12, boasts a more powerful turboprop engine, and carries up to eight passengers, along with two pilots. Its maximum takeoff weight is about 10,500 pounds. The immensely popular aircraft is built in Switzerland with a Pratt & Whitney PT6A-67P engine and sustains a cruise speed of over 300 MPH. It is well known for its safety and reliability.
And the remote-controlled tug just picked up its nose.
Ben guides the PC-12 from its hangar as Steve assumes the job of “wing watcher.” He keeps his eyes on the wing tips to be sure they don’t touch hangar walls inside or walls and other aircraft outside as it makes its way out on the tarmac. Painted lines help Ben guide the plane down the center of the aisle. Once positioned, chocks are returned front and back of one of the rear wheels to prevent possible movement.
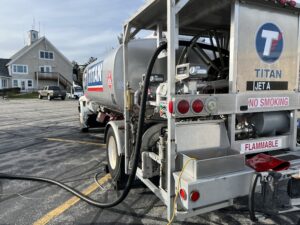
Shoreline Aviation’s jet fuel truck is used by the line crew to fuel both jet and turboprop aircraft.
Fill ’er up!
Now it’s time to fuel the plane. The Pilatus runs a turboprop, which is a turbine engine that drives a propellor instead of generating thrust like a jet. It burns jet fuel, unlike traditional prop planes that burn gasoline.
Before Steve can move the fuel truck to the Pilatus, he goes through a safety check process. This day, the fuel truck has already been filled at the recently built fuel farm, behind the hangars.
Steve first logs his usage needs at the operations desk in the terminal building. The amount of fuel necessary for the planned flight is calculated by a flight logistics specialist – at Shoreline, that’s most often Logan Timpany. Logan is responsible for oversight of the safety of all aircraft going out from Shoreline, from monitoring the weather to ensure fuel loads are correct to making sure aircraft are within weight and balance limits.
“We sump the main tank from this sump port, and I check the quality of the fuel,” Steve says, out at the fuel truck, giving a tube of withdrawn jet fuel a close look. “I make sure there’s no water or any contaminants that shouldn’t be in the fuel. We also check another sump in the rear, that’s through the filters of the truck, making sure it’s nice and clean. We have a check list to go through. Once that’s all done, we can start fueling aircraft for the day.”
Inspections aren’t over yet, though. Next, Steve inspects the fuel truck itself.
“I want to make sure that behind me is completely clear, that there’s no vehicles or aircraft in my way,” he says, starting his walkaround. “I make sure all the cabinets are closed. This truck has air brakes, so we have to make sure this valve is closed – or we won’t have any brakes. Finally, we check that the battery switch is turned on to be able to start the truck. Once I conclude my walkaround and everything is good to go, I can start the truck and we’ll be on our way.”
Safety first
If it sounds like overkill, it isn’t. In aviation generally, and at Shoreline Aviation specifically, safety is Rule-1 for everyone on the team. And an aircraft’s safety begins with the line crew. It involves the maintenance department and the pilots, for sure. But the line team is first up, each and every day.
Like with aircraft, fuel truck wheels are left chocked and then unchocked to move and chocked again when parked at the aircraft.
Before filling the fuel tanks, Steve dons heavy rubber gloves and attaches a ground wire to an unpainted area on the aircraft wheel. He places a protective rubber mat around the fuel port on top of the wing. He climbs a stepladder kept on the truck, carefully inserts the nozzle into the fuel port, and begins filling.
As this is an “overwing” filling, he is sure to pump slowly to avoid spillage. The spring-loaded switch will automatically turn the pump off if he accidentally loses grip of the fueling handle. He fills to the volume level calculated by Logan, and then repeats the process with the tank on the other wing.
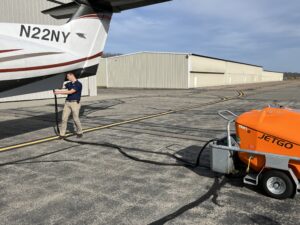
Assistant Airport Manager Ben Garman plugs the Jetgo ground power unit into the Pilatus.
Charge it
Meanwhile, Ben has brought out the Jetgo GPU, or ground power unit. It’s basically a generator that supplies electrical power for starting the aircraft engine so as not to use its battery power so robustly. The GPU roaring, he plugs it into an outlet on the left side of the plane’s tail.
“And now, we’re ready to go,” he says.
All that’s left is for the pilots to climb into the cockpit – there are no outbound passengers on this trip – and go through their checklists. The line guys communicate with the pilots with hand signals. When all is ready, the pilots crank the engine with the running GPU, and the powerful Pratt & Whitney turbine powers up. Ben disconnects the GPU, and Steve signals to the pilots all clear.
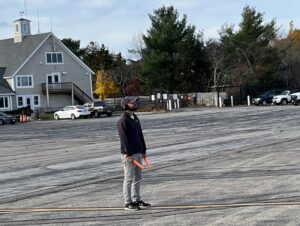
Line Service Manager Steve Dery serves as the marshal to direct the Pilatus PC-12NG from the ramp to the taxi runway.
When the pilots signal they’re ready, the marshal – in this case it’s Steve – directs them with hand-held wands to proceed forward and then turn away from the ramp along a painted centerline and onto the taxi runway. After more system checks, the Pilatus goes to the end of Runway 24 to prepare for a westward takeoff – going into the wind for lift. The big turbine roars to life, the Pilatus builds speed, and this magnificent aircraft powers into the air.
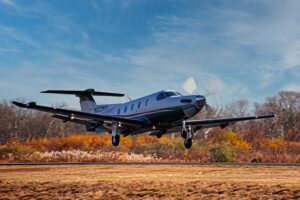
Shoreline Aviation’s charter fleet Pilatus PC-12NG takes off.
Ben and Steve put away the equipment, tidy up, and prepare to prep the next aircraft. Safely, efficiently, and without rushing.
Back to News